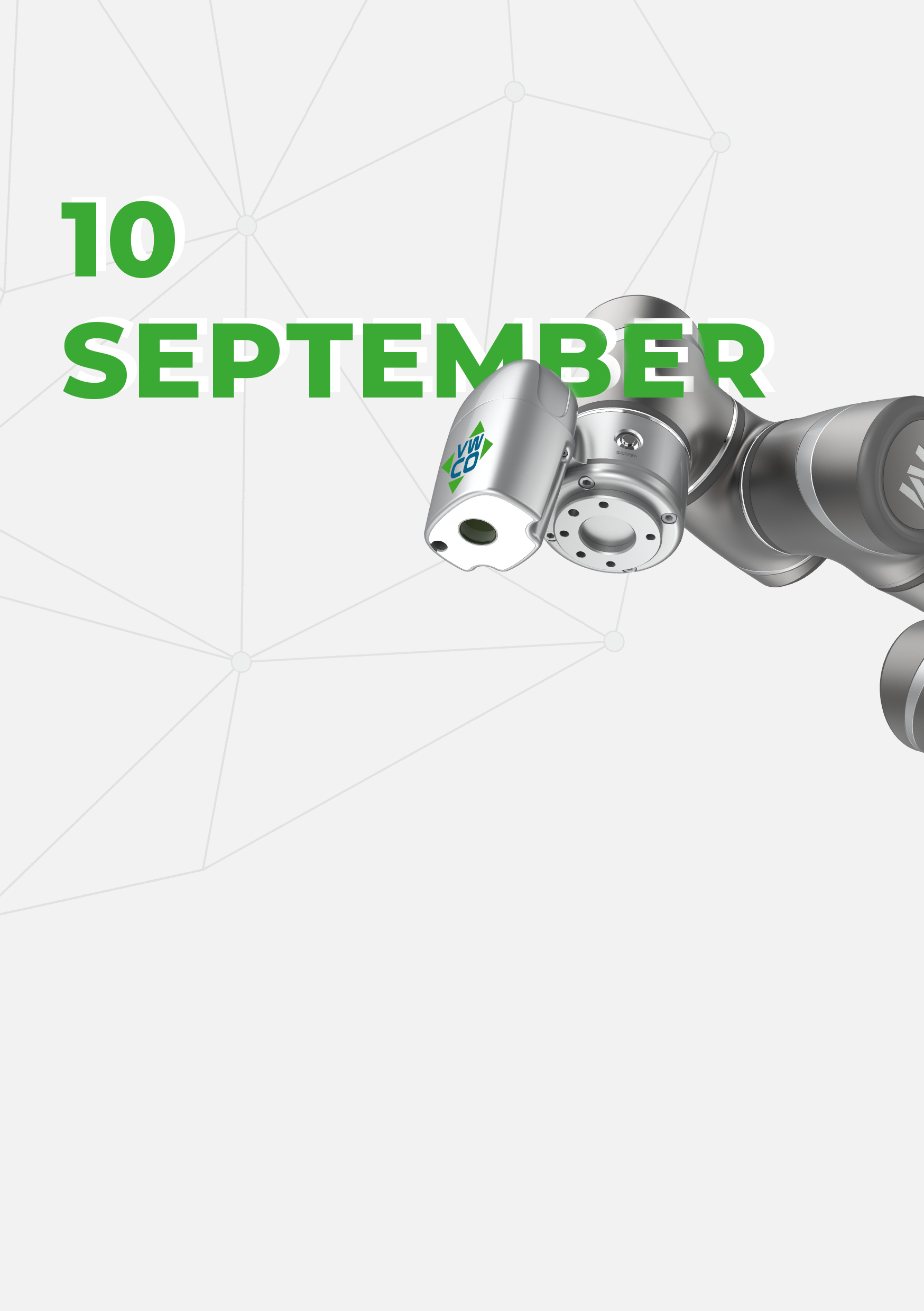
Whether cobots are also the solution to help smaller SMEs with welding automation was also a question that the welding robot integrator from Alblasserdam was concerned with. CCO Pittomvils: "Welding with a cobot is widely presented as super-easy and cheap, but also has many limitations compared to robotic welding. Most welding cobots are now offered as complete cells, complete with welding torch, power source, interface and software. However, the price then comes very close to that of a real welding robot. We see that customers then opt for a welding robot since it offers more possibilities in terms of welding technology, output, future expansion and life span. Programming a welding robot is also becoming increasingly simple."
Turning a cobot into a welding robot is therefore not the right solution to lower the entry level to welding automation, according to the welding robot integrator. "To redo the development process of 30 years of welding robots for cobots is going backwards. We see deployment of the cobot in the welding process rather as a replacement of the manual welder for very simple work. We have therefore developed a solution to connect a manual welding machine, that the customer already has and knows how to use, to a cobot. A perfect solution for companies that already have welding machines and want to automate at a low investment," Pittomvils explains.
Or a real welding robot after all?
For those orienting themselves in the field of welding automation, they now have the choice between a welding cobot from VWCO for a very low investment, a complete welding cobot cell or a welding robot in a higher but equal price range. "Both concepts have their place in the market, but we must keep the expectations of both separate. Panasonic is the only manufacturer that has developed its robots specifically for the welding process. Wire motor, power source and control are fully integrated into it, so that previously impossible processes and features become possible and boundaries are pushed," says Peter Pittomvils. "With this, the way was open in the past decades to develop different solutions for specific welding processes, for welding thin and thick-walled materials, aluminum, stainless steel, etc., among other things. You can't expect all this from a solution with a cobot.".
Short payback period
"Such a high-end welding robot have often a payback time as little as one year." explains Peter Pittomvils. "Then you also have at your disposal the possibilities that we as welding robot specialists develop in the field of automation of the programming process and monitoring of the welding production. Technology that is at a higher level than cobot welding. So our message is to carefully consider which technology you choose for the coming years when you want to automate your welding. If you are sure that it will remain very simple then a welding cobot is certainly interesting, if you want to grow your welding automation just like your company does in the coming years then a welding robot is the right choice."